By Rita C. Peters - Pharmaceutical Technology - Volume 42, Issue 3, pg 18–21
While some drug innovations are the result of surprises during research phases, a surprise that occurs during development--such as formulation or manufacturing problems--could result in approval delays or failure for a drug product.
To reduce the risk of late-phase surprises, some experts recommend that additional screening efforts in early development can smooth the pathway in later development stages. Developers of promising compounds emerging from drug discovery must balance the need to better understand potential formulation challenges and the manufacturability of the drug product with the reality of time and budget constraints.
For investigational new drug applications, drug owners are expected to provide information about the pharmacological and toxicological effects of a prospective drug product, as well as its physical, chemical, or biological characteristics and the stability of the drug substance during the toxicological studies and planned clinical studies. The application also requires information about inactive components planned for the drug product and “any reasonable variations that may be expected during the investigational stage” (1).
In the regulations, FDA notes that “modifications to the method of preparation of the new drug substance and dosage form and changes in the dosage form itself are likely as the investigation progresses” (1). For a Phase I submission, drug companies should focus on the identification and control of raw materials and the new drug substance, the Code specifies; the agency does not expect final specifications for the drug substance and drug product until the end of the investigational process.
For drug development companies, particularly small startups, the focus is often short-term: get the compound to clinic or get an investor or buyer interested in the potential drug. This approach can be short-sighted, experts note, and drug companies would be better served by focusing on getting the drug to market. In presentations, consultants and representatives of contract development and manufacturing organizations (CDMOs) proposed that moving some formulation steps normally conducted in Phase I or Phase II to the preclinical stage can help identify potential formulation and manufacturability roadblocks earlier in the development process and avoid later problems.

Mar 02, 2018
By Rita C. Peters
Pharmaceutical Technology
Volume 42, Issue 3, pg 18–21
Quality by Design - a Practical Approach
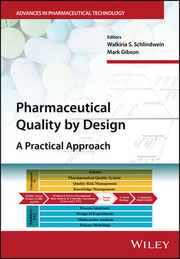
In connection to the above article this book might be of interest.
"Pharmaceutical Quality by Design: A Practical Approach outlines a new and proven approach to pharmaceutical product development which is now being rolled out across the pharmaceutical industry internationally. Written by experts in the field, the text explores the QbD approach to product development. This innovative approach is based on the application of product and process understanding underpinned by a systematic methodology which can enable pharmaceutical companies to ensure that quality is built into the product."