Particle design via spherical agglomeration is a size enlargement technique used in various bulk and fine chemical industries, with recent interest extending into pharmaceuticals, in which an immiscible bridging liquid is added to agglomerate crystals prior to deliquoring. Spherical agglomeration has the potential to dramatically simplify downstream processing, and improves the handling of difficult, needle-shaped crystals. This review consolidates the understanding of the controlling process parameters, identifies the rate processes that control agglomerate attributes, and examines the modelling approaches taken in the literature to optimise the design of such systems. The most important controlling parameters are solvent system composition (requiring knowledge of the ternary phase diagram) and bridging liquid to solid ratio (BSR). Agglomerate size is a highly non-linear function of BSR with many literature systems showing qualitatively similar behaviour. However, there is no method to predict the optimum BSR. Other important process parameters are temperature, constituent particle properties, agitation rate and batch/residence time. Each parameter can have significant effects on the final agglomerate properties including agglomerate size, porosity, strength and dissolution profile.
The rate processes in spherical agglomeration are analogous to those in wet granulation. A general classification of rate processes is proposed in this review including nucleation by distribution or immersion, consolidation, coalescence, layered growth and breakage. While many papers give proof of concept examples of spherical agglomeration for specific systems, only a few have focused explicitly on mechanistic understanding. There is significant scope for further work to quantify the effect of both process parameters and formulation properties on these rate processes. Recent developments in on-line monitoring using process analytical technologies (PAT) should enable these studies.
Using the mechanistic understanding, population balance models can be developed to include kernels for each of the relevant rate processes. Such models should be powerful tools of process optimisation and model driven design with reduced experiments at all scales.
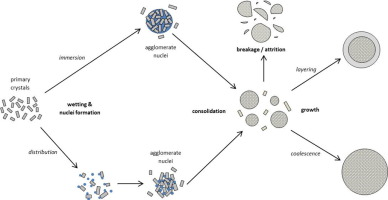